近年来,汽车召回事件层出不穷。召回的原因多种多样,其中,装配过程中因螺栓未正确拧紧导致使用过程中可能出现失效、松动或脱落是原因之一。近日,保时捷(中国)汽车销售有限公司就宣布因供应商制造过程中前桥差速器支架上的螺纹接头可能未按照规定的力矩拧紧,召回部分进口2020款保时捷911 Carrera 4S系列汽车,这种质量事故必然会造成客户对品牌的信任度大打折扣。
时间再往前,2019年宝马(中国)汽车贸易有限公司曾宣布因轮毂螺栓拧紧力矩未达标,召回部分高端X系列汽车。此外,在过去几年里,包括大众、丰田、奔驰等汽车品牌也都曾因生产制造过程中螺栓未正确拧紧而宣布召回旗下部分汽车。螺栓虽小,但因未正确拧紧而产生的安全风险可不小。那么,该如何确保螺栓正确拧紧,不会出现松脱或失效呢?这背后实际上隐藏着大大的学问。
1
拧紧技术与方法
工件与工件的连接有不同的方式,如铆接、焊接、胶接、螺纹连接等。其中,螺纹连接由于具有零部件标准化、装配简单、拆卸方便、效率高且成本低等优点,是机械装配制造领域最基础、标准化程度最高、应用也非常普遍的一种连接方式。而绝大多数螺纹连接在装配时都必须拧紧,这也使得拧紧装配技术成为工业装配与连接技术的重要技术之一。
螺纹连接包括螺栓连接、双头螺柱连接,螺钉连接和紧定螺钉连接四种基本类型。螺纹连接的目的是通过拧紧螺栓/螺母,将被连接件可靠地连接在一起。
装配拧紧的实质是控制拧紧过程中的轴向预紧力,增强连接的刚性和紧密性,以防松和防滑。预紧力,即螺纹连接在承受工作载荷之前预先施加的作用力,是螺纹连接的重要参数,直接影响着螺纹连接的质量。过大或过小的预紧力都是有害的:预紧力过大会造成螺栓被拧断,被连接件被压碎、扭曲或断裂等严重后果;预紧力不足则会导致被连接件错位、歪斜,螺母松脱,甚至紧固件被剪断。因此,拧紧过程中,对预紧力大小、准确度的把握十分重要。
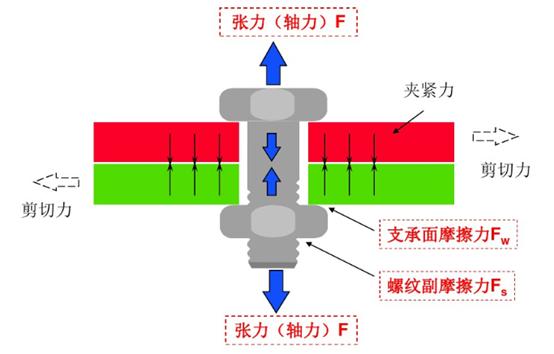
螺纹紧固件受力分析
然而,在螺纹连接的实际拧紧过程中, 无论是两个被连接件间的夹紧力,还是螺纹上的轴向预紧力,在工作现场都很难直接检测,只能通过控制与预紧力相关的其他参数(如扭矩、螺栓头或螺母转角、螺栓伸长量)来间接控制预紧力。因此,通过控制这些参数来间接控制预紧力,正是螺纹拧紧技术的原理。
(一)螺纹拧紧控制方法
目前常见的拧紧控制方法主要有扭矩控制法(T)、扭矩-转角控制法(TA)、屈服点控制法(TG)、落座点-转角控制法(SPA)和螺栓伸长量控制法(QA)等,每种控制方法各有优缺点。
扭矩法操作简单、成本低,拧紧工具相对便宜,扭矩容易测量和控制,扭矩事后易复检,但预紧力离散度大,受摩擦系数偏差影响大,控制精度低,也不能充分利用材料的潜力。
扭矩-转角控制法可以获得较大的螺栓轴向预紧力,且数值可集中分布于平均值附近,但较难确定规定扭矩和角度这两个参数,也较难找出合适的方法对拧紧结果进行复检防错,对拧紧工具要求也较高。
屈服点控制法则不受扭矩控制法的摩擦系数和转角控制法的转角起始点的影响,将摩擦系数不同的螺栓都拧紧至屈服点,可最大限度发挥螺纹件强度的潜力,克服扭矩控制法和转角控制法的致命缺点,提高装配精度;但缺点是对干扰因素比较敏感,对螺栓性能及结构设计要求极高,控制难度较大,价格十分昂贵。
与扭矩-转角控制法相比,落座点-转角控制法则能克服以某一预扭矩点为转角的起点时已产生的误差,进一步提高拧紧精度,但目前应用还比较少。而螺栓伸长量控制法,用于控制法兰螺拴连接最为合适。
因此,在选择拧紧控制方法之前,首先应明确对连接件的要求、预紧力的精度要求和控制方法的应用场合,然后通过实验与分析找出最合理的方法。
(二)螺纹拧紧的过程监测方法
拧紧控制方法与拧紧监测方法,在拧紧程序中分别起着指挥和检查的作用,二者相辅相成。随着科学技术的发展,拧紧工具从手动到自动,控制系统从简单到复杂,螺纹拧紧也从事后检测结果,到同时监控过程。
通过监控拧紧过程,不仅可以提前检查出螺纹的合格与否,拧紧工具的能力和精度是否正常,也可以检查出紧固件与连接件的连接是否正常,连接件的热处理润滑是否正常。过程监控方法与拧紧控制方法配合使用,主要有扭矩控制-转角监控法以及转角控制-扭矩监控法。
扭矩控制-转角监控法,是在扭矩法基础上发展而来,一般使用自动拧紧设备控制。首先当扭矩达到最终装配扭矩的某个范围内后,拧紧设备变成比前面更慢的转速继续旋紧,一直达到最终装配扭矩值。在第二个动作开始工作时,记录旋转的角度,并监测角度,从而达到在装配的同时检查螺纹副质量的目的。扭矩控制-角监控法,一般用于要求较高的装配部位,比如汽车轮胎螺栓、变速箱与发动机连接、传动轴连接螺栓等。
转角控制-扭矩监控法,首先必须使用扭矩法确定转角控制的起始点,拧紧设备拧到这个点后,转速变慢,并开始计算角度,一直达到要求的角度为止,在计算转角的同时记录并监测扭矩。如果扭矩太大,表明螺栓材料的抗拉强度太高或热处理后材料太硬;如果扭矩太小,表明螺栓材料抗拉强度太低或热处理不好,从而达到监控螺纹材料的目的。
(三)装配扭矩的检测
对装配扭矩进行检测,其实也就是再验证拧紧工具(设备)的准确性,避免螺纹连接件在拧紧过程和拧紧装配完成后出现超拧、漏拧以及拧不足的现象,确保螺纹连接件能正常工作。一般有事后静态测试法和在线动态测试法两种方法。
1.事后静态测试法
事后静态测试法,即事后法,就是装配扭矩的过程完成之后再进行检测。这种方法可以直接测试出螺纹副的装配扭矩。由于这种方法使用的测试工具比较简单,一般精度大于3%的机械式指示扭力扳手或电子式扭力扳手即可。而螺纹副的“事后法”测试又有松开法、标记法和紧固法3种。
松开法,是将装配好的螺纹副用指示式或电子式扭力扳手松开,读出松开时的瞬时值,然后根据经验和试验再乘以一个系数α(系数值一般在1.1-1.6之间),特别要注意的是,千万不能将松开扭矩代替测试扭矩,松开扭矩往往要比装配扭矩小30%左右。这种测试方法误差比较大,除特殊情况外在生产中已很少应用。
标记法,是先将螺栓、螺帽与装配主体或构件之间作好记号,然后将螺纹副松开,并再将螺纹副紧固到标记的位置,读出扭矩值,再乘以一个系数α(系数值一般在0.9-1.1之间),所得值即为检查所得的扭矩。这种方法省事、省力,要求技术水平不高,基本上使螺纹副保持原始的装配扭矩,但不适合有特殊放松功能要求的紧固件,这种方法还有可能使摩擦系数产生变化,对测试值产生意想不到的误差。在检测过程中也很少采用这种方法。
紧固法,是用扭力扳手将装配好的螺纹副进一步紧固,当产生微小的转角时,读出测试扭矩值,再乘以一个系数α(系数值一般在0.9-1.1之间)。这是如今比较常用的一种方法,测试值准确,操作方便。但对测试人员的技术水平和技术熟练程度要求比较高。测试时旋转转角越小越好,否则将造成较大的误差。
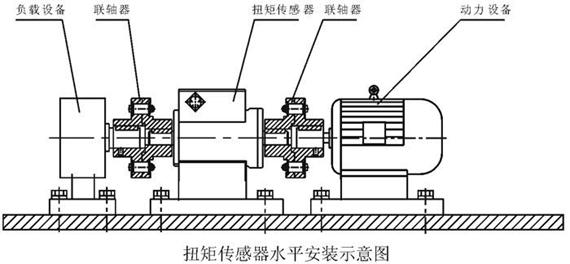
2.在线动态测试法
在线动态测试法,也叫过程法,就是在装配过程中进行检测,一般有四种方法,即传感器直接测量法、固定传感器法、传感器替换法和传感器延伸法。
传感器直接测量法,主要是用扭矩传感器进行检测。一般是将扭矩传感器直接连接在动力头(气动、电动扭力扳手或机电一体化装配机)与螺纹副之间,操作时可以直接读出读数。缺点是由于将传感器随意安装在动力头前面,安装不稳定,有可能不在一条轴线上,从而造成一定的测量误差。
固定传感器法。与直接法的区别是,固定传感器法用于检测的扭矩传感器不是临时安装的,而是固定在动力轴上。固定传感器法是在机电一体化装配机的动力轴上装有2个扭矩传感器,一个用作设备控制,称工作传感器,另一个扭矩传感器专门用作测试,称测试传感器。同时,对测量扭矩传感器备有专门的测试仪器,每隔一段时间,用扭矩测试仪去测试一下测试扭矩传感器,与设备上控制扭矩传感器的数值进行比较。缺点是由于在动力轴上专门安装了一个价值昂贵的测试扭矩传感器,且这个传感器平时不用,只有测试时才用,有点浪费,因此这种方法成本比较高。
传感器替换法,是在机电一体化拧紧装配机的动力轴上安装扭矩测试传感器的部位上,装有一根装卸尺寸与扭矩传感器完全相同的可以快速拆卸的活动轴,当要测试时将快速拆卸活动轴卸下,换上扭矩传感器,然后连接上测试仪器进行测试。这种方法比固定传感器法相比成本低,只需一个扭矩传感器可以在任何动力轴上测试。
传感器延伸法,就是把传感器安装在一个固定的架子上,测量传感器的一端固定不动,而另一端装有可以旋转的轴,在轴上的一端装有模拟的装配螺栓和套筒,另一端与工作传感器相连。当装配机模拟装配时,扭矩直接传到测量传感器上,能比较准确地测出螺栓的装配扭矩。缺点是,由于传感器是固定的,不能测量转角,因此不能测量用转角控制方法装配的螺栓。
02
拧紧工具分类与选型
(一)常见拧紧工具及分类
目前拧紧工具的分类并没有统一的规范。按照使用条件来分,拧紧工具可分为手动工具、气动工具和电动工具。
手动工具主要包括棘轮扳手、开口扳手、快速棘轮扳手、螺丝刀、内六角扳手、定值力矩扳手、开口定扭扳手、表盘/指针式力矩扳手等。气动工具以压缩空气为动力源,主要包括气动螺丝刀(枪式、直柄式、弯角式)、气动扳手(也称“风炮”)等。电动工具则通过电缆/无线实现工具与控制器连接,主要包括电动螺丝刀、电动弯角、电动拧紧机(定扭矩拧紧机/轴,分单轴和多轴组合拧紧机)等。
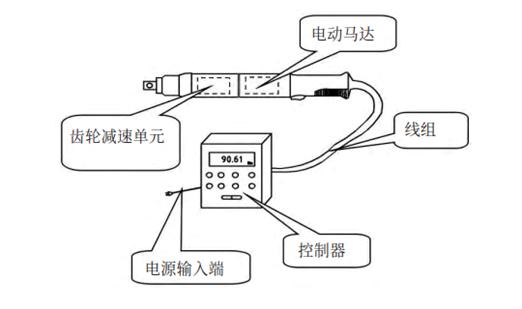
按照扭矩产生方式来分,可把拧紧工具分为直驱式工具、冲击式工具和脉冲式工具。其中,直驱式工具的原理是通过机械行星齿轮组把扭矩力作用于连续的螺栓直到达到目标扭矩,并通过断气机械机构及时切断气源,达到精确控制扭矩目的,优点是精度高,对工位的适用性较好,缺点是有反作用力,如果目标扭矩值过大,需要安装反作用力臂以抵消反作用力,一般用于精度要求较高、连接的适应性要求较高的场合。
冲击式工具原理相当于用锤子击打力臂把扭力传递到螺栓头,类似于刚性材料对刚性材料的敲击,其优点是工具的扭矩重量比较高,无反作用力,价格低;缺点则是易磨损,噪音及震动大,只能用静态力矩扳手进行静态值测量,一般用于精度要求低的场合,常用于拧松螺栓工位。
脉冲式工具原理是通过油压脉冲单元对敲打力进行传递,马达的扭矩在液压体系中靠脉冲进行传递,大大减少了噪声和震动,其优点是工具小巧、人机工程学好,无反作用力;缺点是需要定期补充油压脉冲单元油量,极限节拍差,易过热停机,且连接的适合性有一定限制,主要适用于有一定精度要求,无反作用力的工位。
(二)自动拧紧系统
近年来,由于装配环节精密化、自动化、智能化的需求驱动,对拧紧操作的自动化、智能化、规范化以及拧紧数据的可追溯要求也越来越高,因此自动化的拧紧技术也得到了广泛应用。
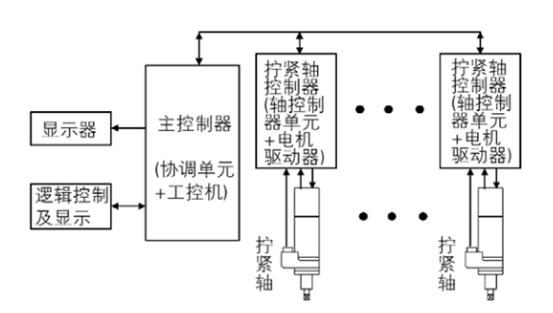
伺服拧紧机结构及原理图
自动拧紧技术需要自动控制的拧紧工具,目前比较常见的是伺服拧紧系统。伺服拧紧系统一般由上位工控机、专用轴控制模块、驱动执行单元和检测单元等部分组成。驱动执行单元直接对螺栓进行拧紧等各种操作,并通过检测单元把拧紧的过程变化量和状态变化量反馈给控制单元;控制单元又与驱动执行单元相连接,按照接受到的参数直接对其操作,并实时将拧紧轴的特性数据和采集到的实时数据传递给上位工控机,以便实现显示、设定、存储等,既能保证拧紧达到螺栓的最大状态,也能保证螺栓不会因超出屈服强度而发生变形、断裂等失效。
此外,工业机器人搭载拧紧模组的机器人自动拧紧装配解决方案也逐渐被应用。比如,马头动力工具开发的零部件螺栓在线全自动拧紧系统,由工业机器人、拧紧机构、行程机构和送钉机构组成,可以实现拧紧点定位、轴间变距,兼容不同种机型,多种规格螺栓装配的柔性化装配,可用于动力总成、汽车零部件、新能源电池PACK组装、家电装配等工业领域。
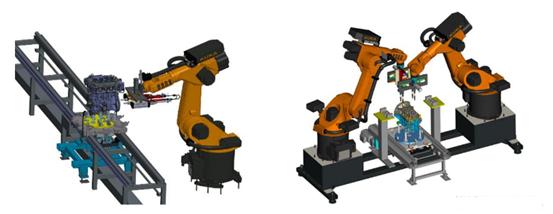
(三)拧紧工具选型
市面上拧紧工具种类繁多,拧紧控制方法也不一。对于拧紧工具的具体选型,一般在明确自身对拧紧工具的具体需求后,可从拧紧工具本身以及拧紧工具厂商两个维度进行综合选型。一方面,企业应根据自身需求,如对转速(工具最高转速决定了装配效率)、动力源(手动、气动或电动,以及洁净度要求等)、精度/追溯(对精度的要求以及拧紧数据是否可追溯)、拧紧策略(如扭矩控制法、扭矩-转角控制法、屈服点控制法等)、应用成本等方面的要求进行工具的具体选型;另一方面也应对拧紧工具厂商的非标/项目管理能力、工艺优化支持能力以及售后服务能力等进行综合评估和考量。
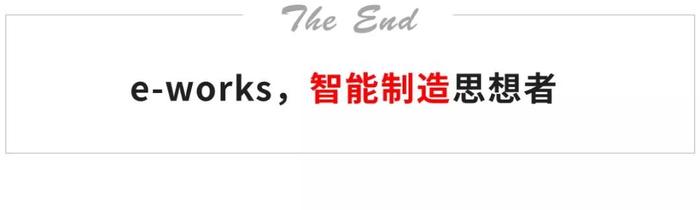
财经自媒体联盟 更多自媒体作者
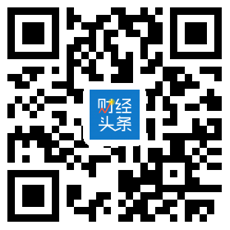
新浪财经头条意见反馈留言板
4000520066 欢迎批评指正
All Rights Reserved 新浪公司 版权所有